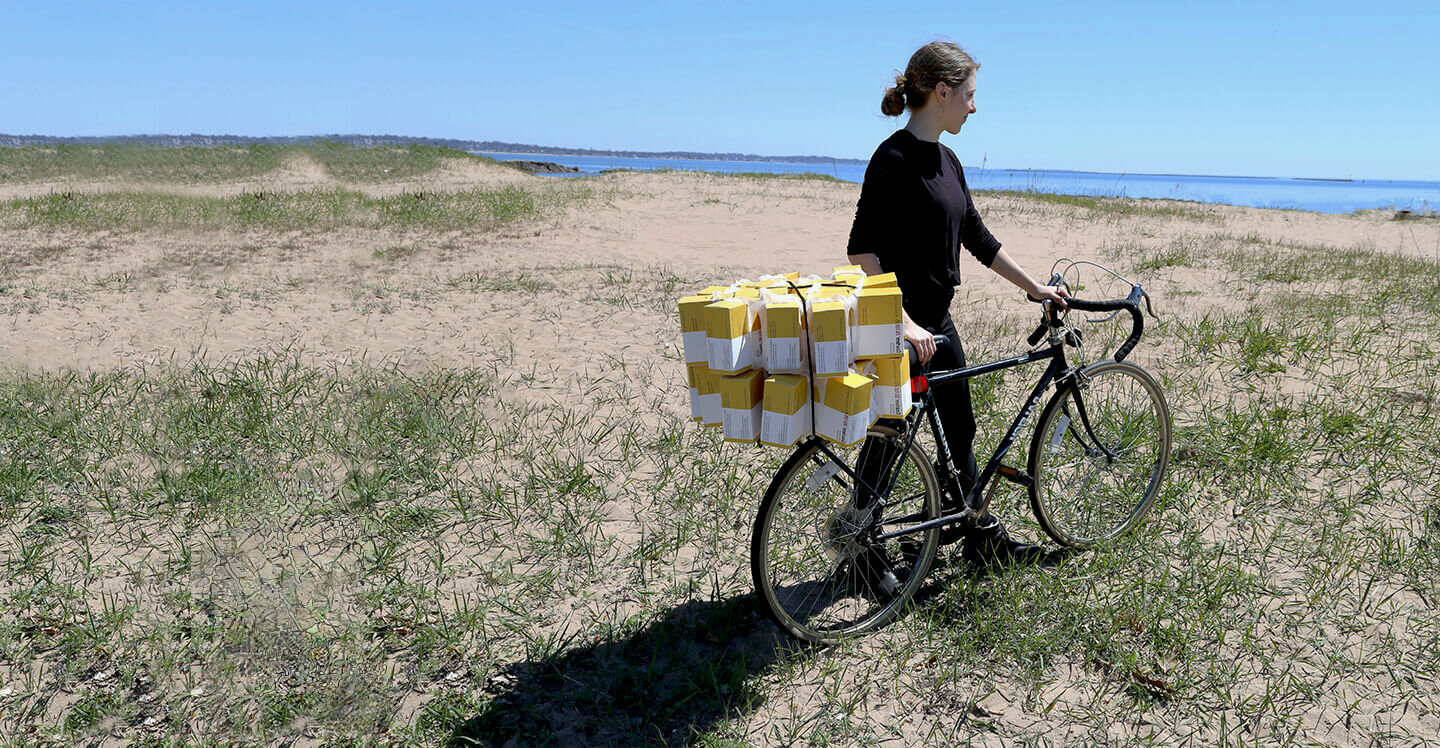
VeloMed
A packaging system to enable easier and more efficient medication delivery.
Radically expand the capabilities of last-mile delivery.
The Problem
Medication isn’t getting where it needs to go.
In large regions of sub-Saharan Africa, there are few options for distributing medication to rural health posts. As a result, populations in these areas can go weeks or months without access to essential treatments. Because certain medications are not consistently available, millions of people die from treatable diseases like malaria and diarrhea every year.
Isolated populations rely on a set of volunteer health workers to pick up boxes of medication from urban centers and deliver them to remote clinics. These volunteers have little to no access to transportation and typically do these deliveries on foot or by bike.
The barrier is limited capacity.
Volunteer health workers must transport boxes using whatever they already own, typically a backpack or small bag. But a backpack can only fit around 7 boxes at a time and this medication may need to cover hundreds of people in a single community.
A packaging solution to limited capacity.
VeloMed, a thin plastic packaging system, provides a cost-effective way to increase carrying capacity without the need for large-scale infrastructure change. With VeloMed community health workers who were previously limited to 5-7 medication boxes per trip, could now transport more than 45 boxes at once.
700% increase in capacity
With VeloMed, community health workers can transport enough medication for an entire community in a single trip.
Intervention through packaging
VeloMed is low in cost but high in impact, addressing two critical issues in the current system – inefficient last-mile delivery and a lack of storage and organization in rural clinics.
Cost-effective and intuitive.
Keeping costs low is essential to the viability of any solution in low-resourced settings. VeloMed is made from thin, photo-degrading polyethylene, making it cheap and easy to manufacture.
Visually tracks supply levels.
Once medication arrives at a rural clinic, the VeloMed strip can be used as an organizational tool. Hung on the wall, it serves as a visual record of how much medication is in stock. This allows volunteers to more easily plan their next medication delivery.
A realistic solution is cost-effective, easy to distribute with limited infrastructure and intuitive to use with minimal guidance.
Leveraging existing structures
A solution that requires a large change in local infrastructure (eg. more vehicles, better roads, etc) is simply unrealistic for an already resource-deprived setting. VeloMed does not require any change to the current medication delivery system in recipient countries and necessitates only a minor adjustment at the manufacturing-level.
Easily integrated into current supply chains.
VeloMed, is already compatible with the existing manufacturing and global delivery system. The lightweight and compact VeloMed strip is cheap to produce and easily slipped into existing medication shipments.
Empowers community health workers.
VeloMed does not require any change in the workforce, but rather makes the existing workforce more efficient. Because VeloMed is included with medication shipments, there is no extra burden on community workers to purchase or acquire anything extra.
How it works
Cut to size + fill by hand.
Once the medication arrives at a distribution hub, the strip is cut to the desired length and filled by hand. The 14mil low-density polyethylene is perfectly calibrated to hold boxes securely and still be easily applied by hand.
The filled strips are then rolled into compact units.
The units can be stacked and secured to a bike with a cord.
Case Study:
Malaria isn’t supposed to be a death sentence.
Every year, malaria kills half a million people who fail to receive treatment in time.
The delivery of medication is a critical step in the treatment life cycle. For the majority of patients, malaria can be treated with a free 3-day course of medication. Despite widespread awareness of this treatment, half a million people die from the disease annually - 90% of whom live in Sub-Saharan Africa.
In many rural areas in this region, community health volunteers can travel to individual homes to test and treat malaria, expanding access and reducing the burden on clinics. Their ability to treat malaria patients is bound by their individual carrying capacity.
The malaria infection and treatment life cycle. On the left is the life cycle of a malaria infection and on the right is the process of re-stocking medication at a remote clinic.
Prototyping
Several mechanisms, forms and materials were explored to arrive at the final design. Here are just a few of the models made along the way!
Focus on expandability
To create a tool that could expand to accommodate various loads, I first explored collapsible structures drawing on morphology, origami, etc.
Focus on minimal material
Many of the early prototypes were ultimately too complex or required excessive material. This made them unrealistic interventions for a low-resourced setting. To develop a more realistic solution I shifted my focus to minimal-material options.
Shift to a packaging solution
In order to shift the burden off the community health worker, I decided to target my intervention at the manufacturing level, with a packaging solution. Inspired by six-pack rings used to transport cans, I experimented with applying that principle to boxes. I tested dozens of cutout shapes and materials to find a combination that was easy to use and had excellent grip. Ultimately, I chose a dog-bone-shaped cutout with curved corners that stretch to grip the box and tabs that prevent it from slipping backwards. For the material, I settled on a 14mil low-density polyethylene because its tensile strength allows it to be stretched by hand, but it is stiff enough to hold securely.
Dutch Design Week
Antenna selection as “One of the World’s Best Design Graduates”
VeloMed, as well as a related malaria prevention tool, was selected to be part of Design Indaba’s Antenna program, in which 20 of the best design graduates from across the globe are invited to present in a special series at Dutch Design Week. Check out the presentation!
Video of presentation at Dutch Design Week.